CNC Turning
Items processed by this process will be cylindrical and must always be on-centre. Turned parts range from simple rings to complex curved shapes. In addition, mass-parts can be produced.
In CNC Turning the workpiece is held in place by an instrument known as the “chuck.” The chuck then spins at many different RPMs. However, this depends on your machine. When this occurs, the machine’s tool moves into the workpiece and shaves away material to create the desired shape.
Many cutting tools can be installed within the lathe tooling head to perform different operations. This is to produce parts in a one process. Straight cuts, tapers and contours can all be created by changing the angle and depth of the cut.
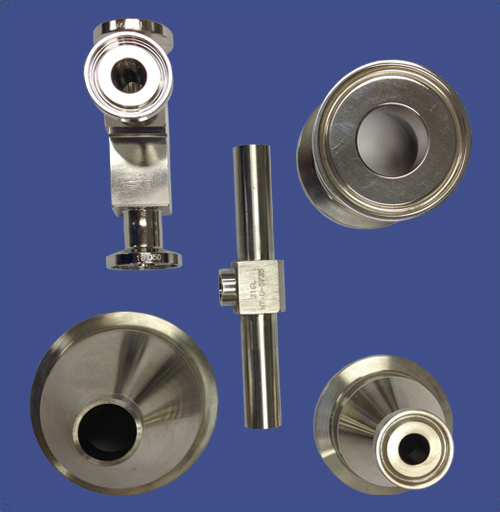
CNC Machining
Today’s CNC Turning and CNC Milling machines are numerically controlled and operate without the constant supervision and adjustment of the turn wheels by the operator. Also, modern machines have various types of tooling options, spindle options, as well as speed and power capabilities. Oftentimes, these machines have tool holders equipped. This holds many tools of different sizes and shapes for various applications depending on the complexity of the part.
What is the difference between CNC Milling and CNC Turning?
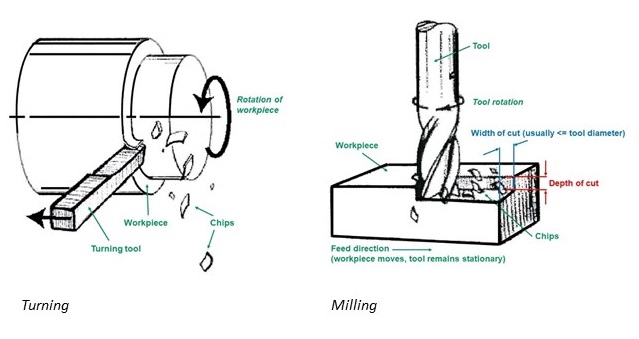
Often CNC Milling and Turning is generically referred to as “CNC machining”.
The difference between the two processes comes down to which part moves. This part being the workpiece or the machine.
Firstly, with turning a metal bar is fed into the lathe and rotates at high speed. Then a single-point cutting tool removes parts of the metal to create the desired shape.
However, With milling the metal usually remains still while multi-point cutting tools rotate around it.