What is Wire Eroding?
Wire Eroding is a precision engineering process where a work piece is cut through with a strand of wire. This process creates electrical sparks between the wire and the work piece and these electrical sparks cut through the work piece. This is a cost-effective method that has Amazing accuracy on thicker material parts. Wire cutting machines can cut complex shapes.
The sparks in Wire Eroding are controlled and in recent years, a special liquid named ‘dielectric deionised water’ is used to make sure the accuracy is correct. This water plays the part as a coolant to make sure the metal components don’t get hot and mess up the process. Also, ‘dielectric deionised water’ is used to wash away any particles that could get in the way of the work piece and the wire. The wire erosion process starts towards the edge of a work piece or by drilling a hole where the process will begin.
The EDM wire eroding process relocates back to 1770. English scientist named Joseph Priestley discovered that electrical discharge could erode metal. Also, This could be used to create desired shapes and designs.
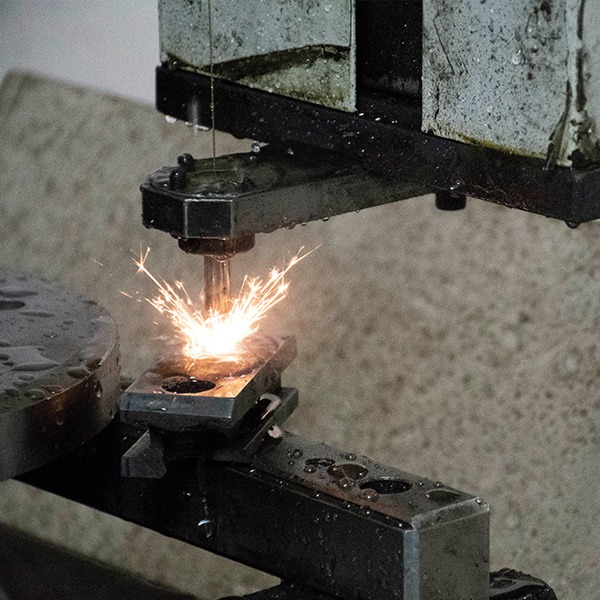
Advantages of this process
- You can achive the best detail possible when using this form of machinery.
- Hard materials do not affect or make the process more difficult.
- It can handle even the smallest of workpieces compared to the more traditional cutting tools which cause damage and leave rough edges.
- There isn’t any direct contact between the tools and workpiece, meaning weaker materials can be machined without it breaking.
- Any surface finish can be obtained.
- Fine holes can easily be drilled.
- Complex cutting can be achieved.
- Wire Erosion doesn’t leave burrs.
EDM wire eroding services
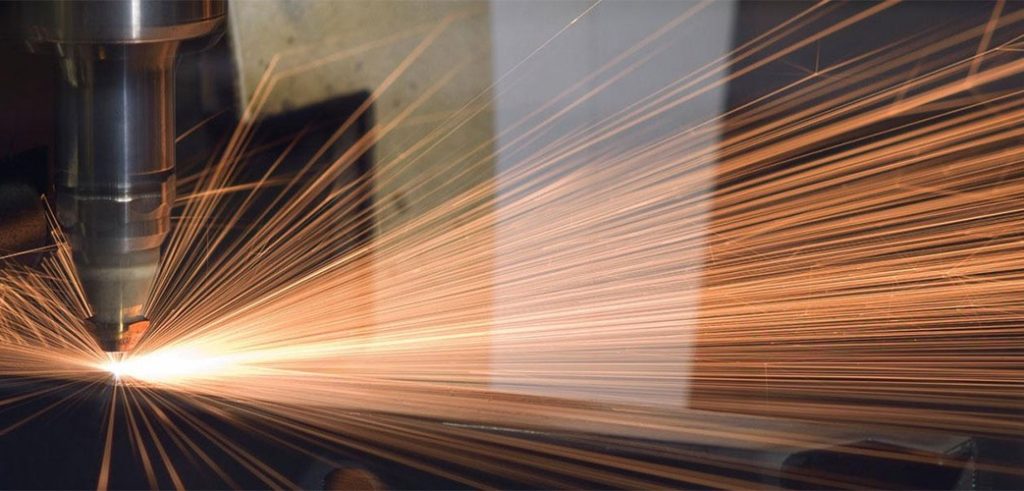
Electrical discharge machining defeats a major issue that is found in contact machining.
Once the desired shape has been cut, the parts are then made harder by a heat treatment. However, This adds time, cost and can alter the finished parts’ dimensions if the heat treatment process is not controlled. The advantage of EDM is that it can cut hardened materials and exotic alloys while also providing the best surface finish.
Firstly, in Wire EDM, the electrode is fed through an upper and lower diamond guide, and then discarded after use. The wire is controlled by a CNC control which allows you to program a path for the wire to travel.